Manufacturing Methods of Felts & Nonwovens
Felts and Nonwovens are fiber products, which are fabrics made by three-dimensionally entangling and bonding fibers.
From among the various manufacturing methods, we introduce our typical processes.
1. Compounding
Raw material fibers are untangled and compounded.
2. Carding
Fibers are carded so that they are parallel to one other and laps are made.
※Click on the manufacturing method you want to know.
Pressed Felt
- Features
- Wool is used as a main raw material. The unique characteristics of wool, such as heat-retaining property, moisture absorption & desorption properties, flame retardancy, water repellency and dyeability, are utilized.
- Uses
- Parts of musical instruments, colored felt, rugs, interlining, gaskets, polishers and etc.
3-1. Hardening
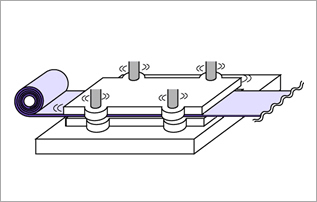
The felting (fulling) property of wool is utilized in this process. Moisture and heat are applied to the laps, and then force is applied to them to entangle fibers.
3-2. Fulling
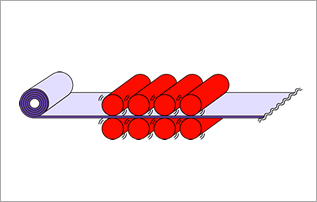
Felt is sandwiched between the upper and lower rolls and compressed to get the specified hardness.
3-3. Dyeing
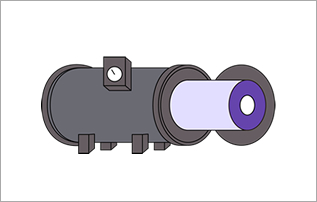
Felt is dyed the specified color.
3-4. Drying
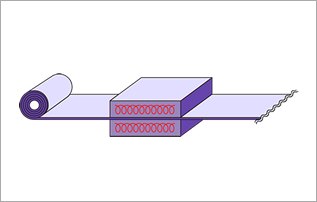
Excess water is removed.
3-5. Pressing
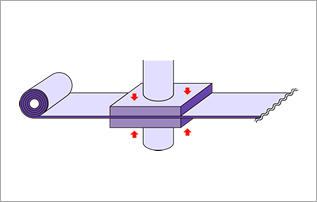
Felt is sandwiched between the heat press plates and the surface is smoothed.
Needle-Punched Nonwovens
- Features
- Various kinds of fibers can be used. We support a wide range of specifications and characteristics, from thin (1mm) to thick (over 10 mm) and from soft to hard.
- Uses
- Filters, industrial materials, padding materials, carpets, interlining and etc.
Thermal-Bonded Nonwovens
- Features
- They require mixing of thermal-adhesive fibers. We support a wide range of specifications from thin to thick by changing fusing method.
- Uses
- Insulators, cleaning materials, cushioning materials, sanitary materials and etc.
Chemical-Bonded Nonwovens
- Features
- Hardness can be changed depending on properties of the adhesive polymers used. It is easy to add value such as flame resistance and deodorant effect by using functional polymers.
- Uses
- Cushioning materials, industrial materials, filters, interlining and etc.
Spunlace Nonwovens
- Features
- The most notable feature is their thinness and soft texture. Because fibers are not damaged much, the surface is smooth.
- Uses
- Cushioning materials, industrial materials, sanitary materials, wiping materials and etc.
4. Inspection
Finished products are inspected to ensure that there are no defects.
Composite Processing
We produce highly functional and high-performance products by applying our wide-range processing technologies to various felts and nonwovens regardless of our products or not.
Cutting
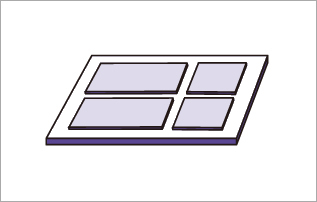
We have particular strengths in cutting precisely in half or in precise size and desired shape according to your specifications.
Sewing
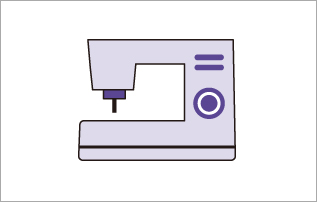
Our sewing technique is excellent in sewing materials in unique shape and can sew to your exact specifications in size and shape.
Slitting
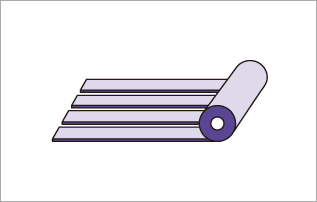
Our slitting machines can slit not only single body of felt and nonwoven but also composite materials as narrow as a few millimeters.
Slicing
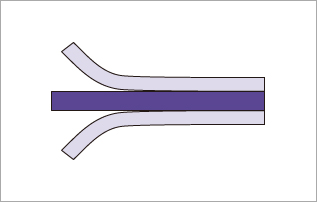
Our technology, which we are proud of, can make felts and nonwovens sliced as thin as several hundred microns of thickness.
Resin Treatment
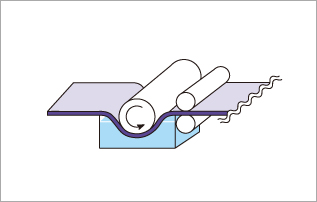
Felts and nonwovens are impregnated with resin and additional functions are available, such as flame resistance and water repellency.
Pleating
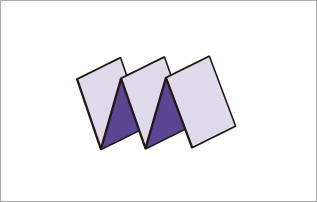
Our pleating machines can fold multi-layer nonwovens with different functions.
Electret processing
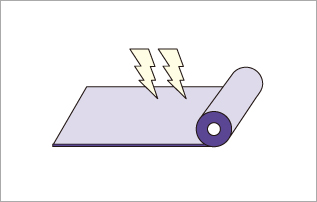
Nonwovens are electrically highly charged and become capable of catching fine dust.