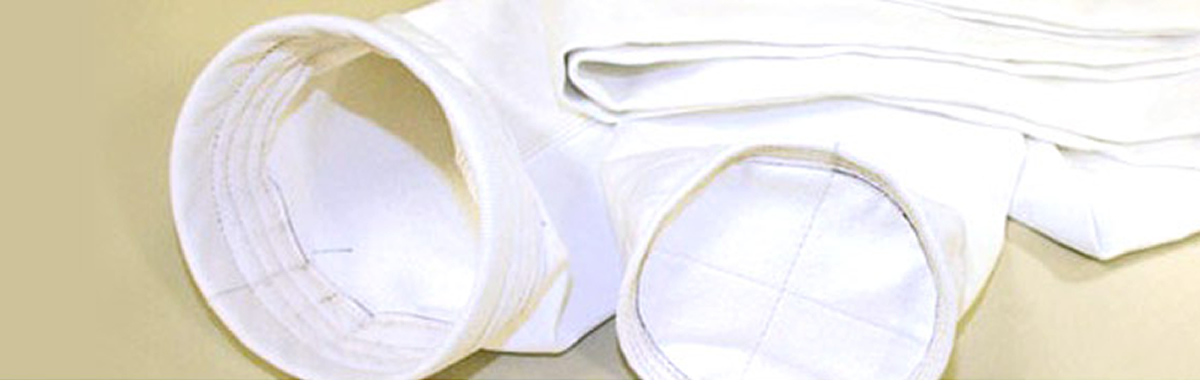
Product Outline
Since launching the first needle-punched felt for filter bags on Japanese market, we have offered a wide variety of products and extended high value-added products.
In particular, ADMIREX is one of the original products made of the finest PTFE fiber.
Raw Materials
Polyester, Meta-aramid, PPS, PTFE, polyimide, polypropylene, acrylic, nylon
ADMIREX™
01. Properties
The most distinctive feature of ADMIREX is a high-performance filter bag and made of its astonishingly fine PTFE fiber developed by Daikin Industries.
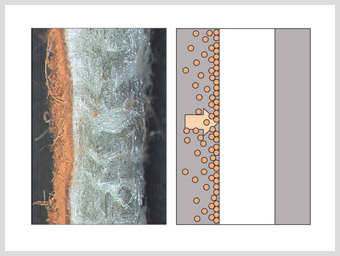
ADMIREX(Surface Filter)
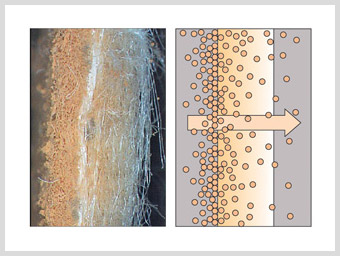
Standard Filter(Depth Filter)
Test Method: JIS11 Kanto Loam Powder (Reddish Brown), After 150 Pulses
- This filter media is made of PTFE fiber which is one of the finest PTFE fibers.
- This filter media has two-layer structure where the upper layer performs filtration and the lower layer performs strength retention.
- The filtration layer forms its fine structure by water jet method.
- No adhesives enables the filtration layer to high porosity.
- Excellent interlayer entanglement prevents from a structural defect such as interlayer separation.
- We can make material selection of the strength retention layer depending on the operating environment.
The filtration layer is made of PTFE fiber which is one of the finest PTFE fibers.
Properties of ADMIREX Fiber
- Extra-fine PTFE fiber with average diameter of 10 micro-meter.
- Fibers with specific range of diameter distribution.
- Fiber with branching and its diameter is a few micro-meter.
- Modified cross-section fiber.
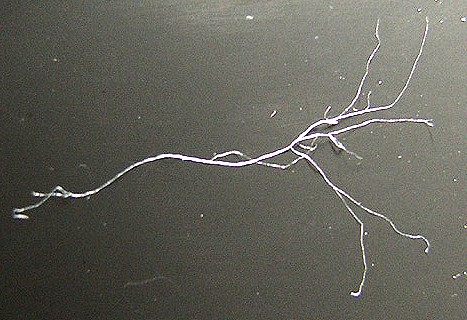
02. Collecting Performance
The fine filtration layer enable to high performance of dust collection.
The advantage of this filter media is to collect fine dust particles.
Test Conditions
- Dust: NaCl (Sodium Chloride)
- Average Particle Diameter: 0.07μm
- Filtration Rate: 2m/min
- Sample Size: 150mm×150mm (Effective Area of 100㎠)
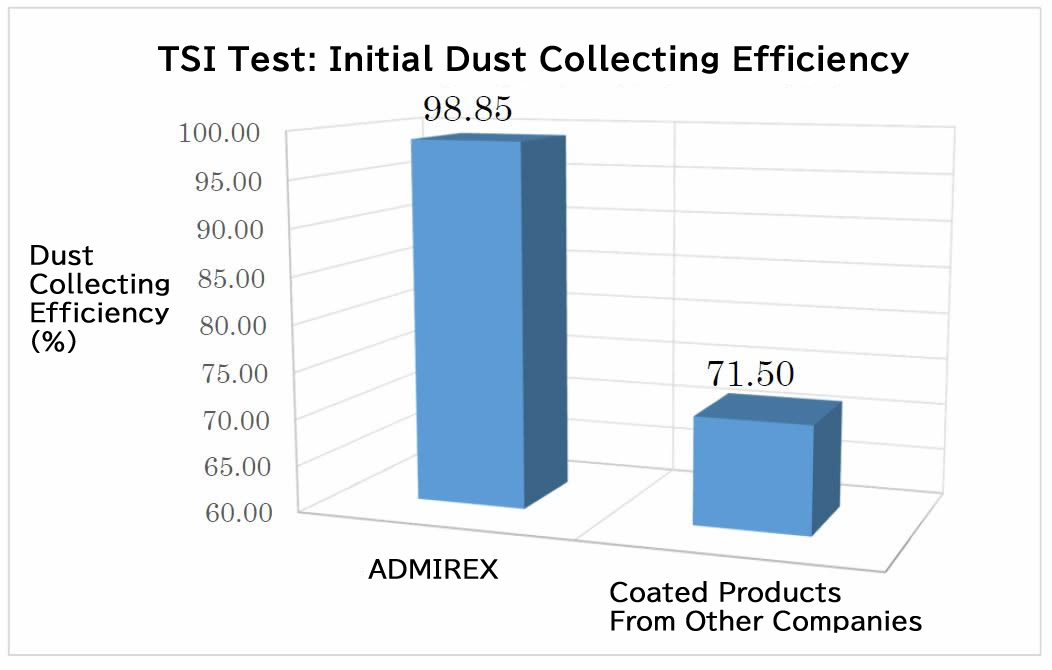
03. Pressure Drop Properties
The optimal filtration layer enables to surface dust collection with low pressure loss.
This leads to reduce the number of reverse airflow called pulse-jet and extend the life expectancy of the filter media.
Performance Evaluation of Filter Bag by Pulse-jet Testing
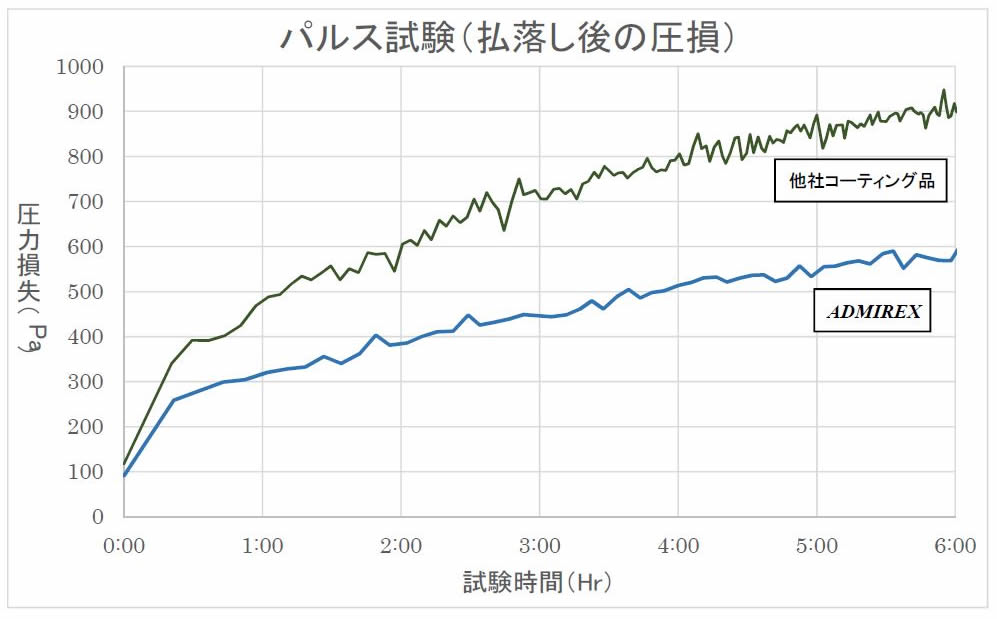
Conforming to JIS Z8909-1
Test Conditions
- Entrance Dust Concentration:5g/㎥
- Filtration Rate:2.7m/min
- Sample Size:164Φ×1000mm(Effective Filtering Area (Suction Area):1㎡)
- Pulse Pressure:0.3MPa
- Temperature:Normal Temperature
Test Method
- Initial Collecting Performance: 6 Hours with a Control of 1,000Pa
Performance Evaluation of Filter Cloth by VDI Testing.
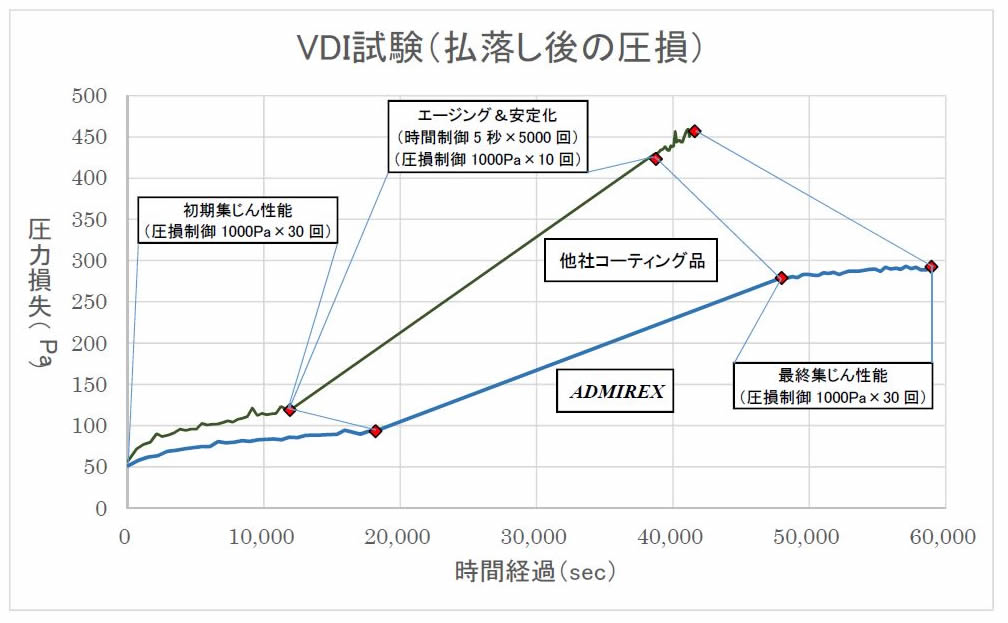
※The complete surface dust collection structure prevents from entering dust into the inside of filter media.
In addition, excellent surface smoothness with PTFE contributes to remove dust from the surface of the filter media.
This dust removing function allows for low pressure operation with small backwashing energy.
Conforming to JIS Z8909-1(VDI Method)
Test Conditions
- Dust: Pural NF (Aluminum Oxide)
- Particle Diameter:3.5~6.5μm
- Entrance Dust Concentration:5g/㎥
- Filtration Rate:2m/min
- Pulse Pressure:0.5MPa
- Sample Size:155Φ×1000mm(Effective Area of 140mmΦ)
- Temperature: Normal Temperature
Test Method
1.Initial Collecting Performance
- 30 Repeated Pulses With a Pressure Drop Control of 1,000Pa
2.Aging and Stabilization
- 5,000 Repeated Pulses With Time Control at 5 Second Intervals
- Then 10 Repeated Pulses With a Pressure Drop Control of 1,000Pa to Stabilize Collecting Performance of the Filter Cloth
3.Final Collecting Performance
- 30 Repeated Pulses With a Pressure Drop Control of 1,000Pa
04. Durability
This filtration layer with around 80 micro-meter thickness has flexibility and excellent strength against stress from pulse-jet.
We had evaluated the tensile strength of the filter media with the actual incinerator under the following conditions.
The less tensile strength degradation after 96,000 pulse-jet means long life of the filter media and to keep the stable operating.
Test Conditions
- Test Plant: Industrial Waste Incinerator
- Test Period: 12 Months
- Pulse Count: 96,000 (The equivalent to 5 years of a general municipal waste incinerator.)
- Pulse Pressure:0.3~0.4MPa
- Exhaust Gas Temperature:180℃
- Tensile Strength: Conforming to JIS Z1096(Unit: daN;50mm cloth)
05. Chemical and Heat Resistance
The filtration layer has acid resistance, alkali resistance, oxidant resistance, organic solvent resistance and all chemicals resistance except fluorine gas, chlorine trifluoride, and molten alkali metals.
Excellent heat resistance of PTFE fibers allows instantaneous maximum operating temperature of 260 ℃.
06. Reactor system
Due to surface smoothness structure and fine pore size structure, the cake layer maintains on the surface of the filtration layer after pulse-jet.
In case of the reactor system, the cake layer acts neutralization of harmful gases.
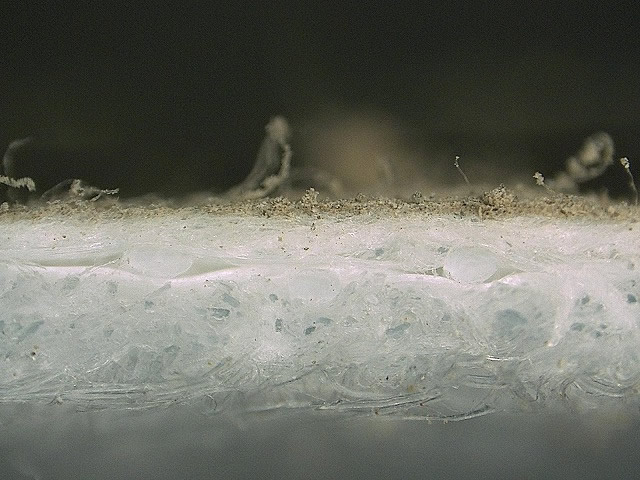
Cross-section of ADMIREX after over 1 year use in a gasification melting furnace.
The dust is collected completely on the surface, and it maintains its uniform cake layer.
※This is data for ADMIREX with the same performance (PTFE felt + PTFE web)
07. Sales Performance
After the launch in 2001, ADMIREX has been recognized for impressive features and installed at many facilities such as municipal waste incinerators, flue gas treatment for incinerators and so on.
In particular, we continue to maintain its reputation for many facilities that handle a number of fine particle dust such as gasification melting furnaces and ash melting furnaces.
Usage
- Dust collectors for the municipal waste incinerator
- Dust collectors for the industrial waste incinerator
- Dust collectors for the ASR incinerator
- Gas-cleaning equipment for top pressure recovery turbine generating system
- Fumed silica collection
- Biomass power plants
Furnace Types
- Stoker furnace
- Fluidized bed furnace
- Gasification melting furnace (shaft, kiln, or fluid bed)
- Ash melting furnace (plasma melting or surface melting)
All the data given in this page are for reference only and are not guarantees on product performance.
Please contact us by our dedicated form for further product information.